Ingenieras de la UVigo ensayan cómo reducir la corrosión mediante la impresión 3D de hormigón
Dos grupos lideran un proyecto nacional que persigue reducir los costes y el impacto ambiental de la construcción con un nuevo método de protección catódica
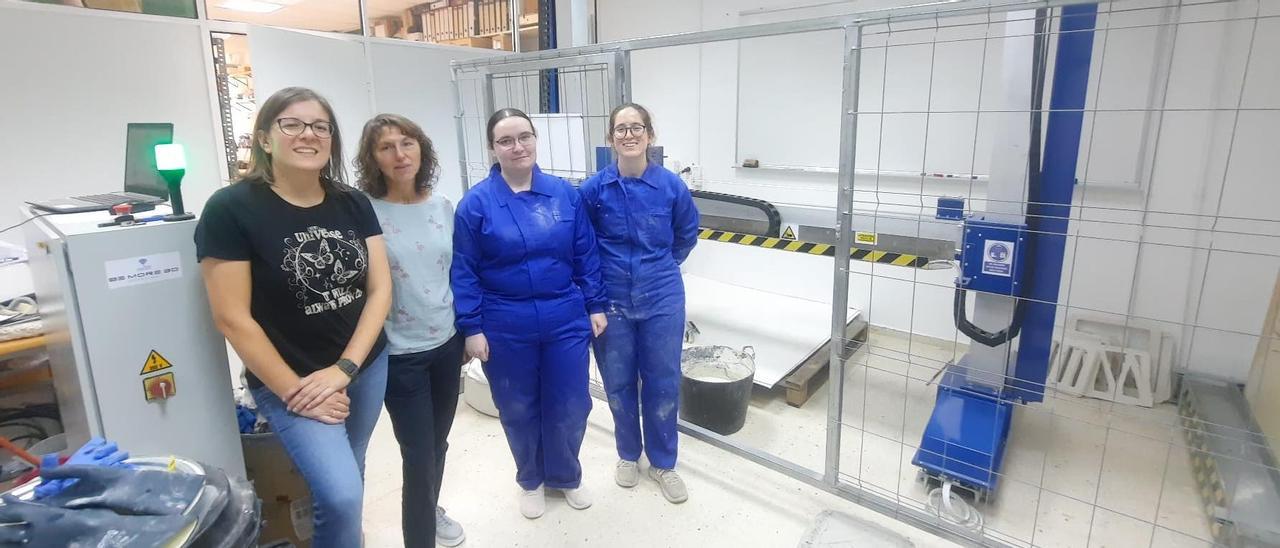
Vídeo: R. Grobas
Ingenieras de la Universidad de Vigo lideran un proyecto nacional que evalúa de forma pionera los beneficios de la impresión 3D para proteger las estructuras y que podría ayudar al sector de la construcción a reducir sus costes y el impacto ambiental. La iniciativa Sustain 3D consiste en la puesta a punto de un método de protección catódica con cementos conductores obtenidos mediante fabricación aditiva, aquí es donde radica la principal novedad y el reto para las investigadoras, y que resultaría más barato que los desarrollados hasta el momento.
El estudio, con una duración de dos años y una financiación de algo más de 150.000 euros a cargo de los Fondos Next Generation, acaba de iniciar las pruebas con una impresora diseñada por la firma Be More 3D y unas dimensiones de 6,5 x 3 metros ampliables. Gracias a este proyecto, Vigo se ha convertido en la única universidad gallega que cuenta un equipamiento creado por esta empresa tecnológica valenciana y la idea es seguir sacándole partido tanto en investigación como en docencia. De hecho, ya la han visitado los alumnos del máster en Fabricación Aditiva que se ha estrenado este curso.
Los dos grupos implicados, Encomat y e-Materiais, surgido del primero, cuentan con una amplia experiencia en el estudio de la corrosión y de las técnicas electroquímicas. Y en este proyecto fabricarán, mediante impresión 3D, cementos conductores que funcionarán como ánodos para la protección y prevención catódica (aplicación de corriente) del hormigón.
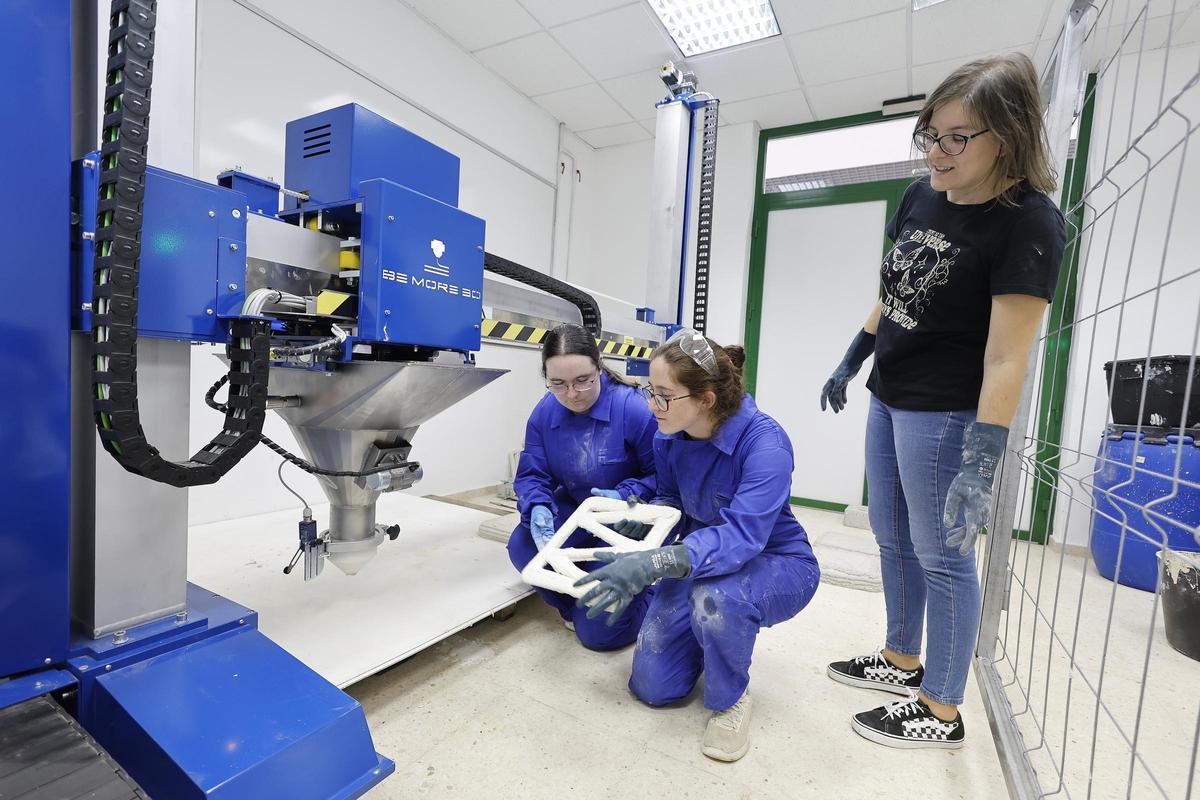
María José Gallego, Carmen Mariño y Belén Díaz (de pie), con una de las piezas impresas. / Ricardo Grobas
“Los cementos conductores utilizan materiales como las fibras de carbono que son muy costosas y por eso no han dado el salto todavía desde el nivel de la investigación para ser implementados en la industria. Nuestro objetivo es sustituir las películas que se aplican actualmente de forma continua sobre las estructuras de hormigón para repararlas, y que incluyen fibra de carbono o titanio, por piezas con distintas geometrías obtenidas mediante fabricación aditiva. De esta forma, ahorramos material y peso, con lo cual no se daña la estructura”, explica Belén Díaz, coordinadora de e-Materiais e investigadora principal del proyecto junto con Carmen Pérez, de Encomat.
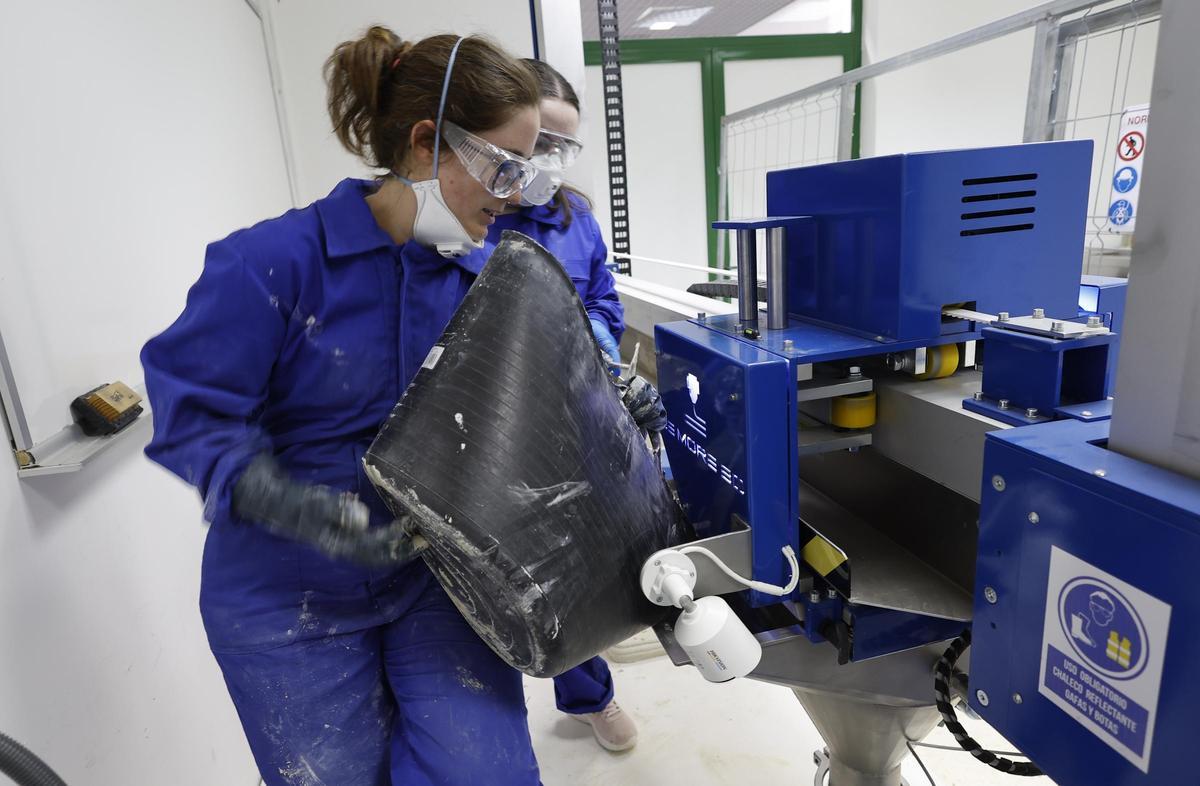
Las investigadoras, durante el vertido del hormigón en la máquina. / Ricardo Grobas
El proyecto implica un gran número de pruebas para llegar a imprimir un cemento que sea conductor. “Tenemos que ajustar muchas cosas porque a medida que añades materiales al hormigón cambias sus propiedades”, apunta Carmen Mariño, ingeniera en Tecnologías Industriales y una de las investigadoras contratadas dentro del proyecto junto con María José Gallego, graduada en Química y con un contrato del programa Investigo del SEPE.
También forman parte del grupo de trabajo Xosé Ramón Nóvoa, responsable del grupo Encomat, y Antonio Collazo, coordinador del máster en Fabricación Aditiva que imparte la UVigo de manera conjunta con A Coruña.
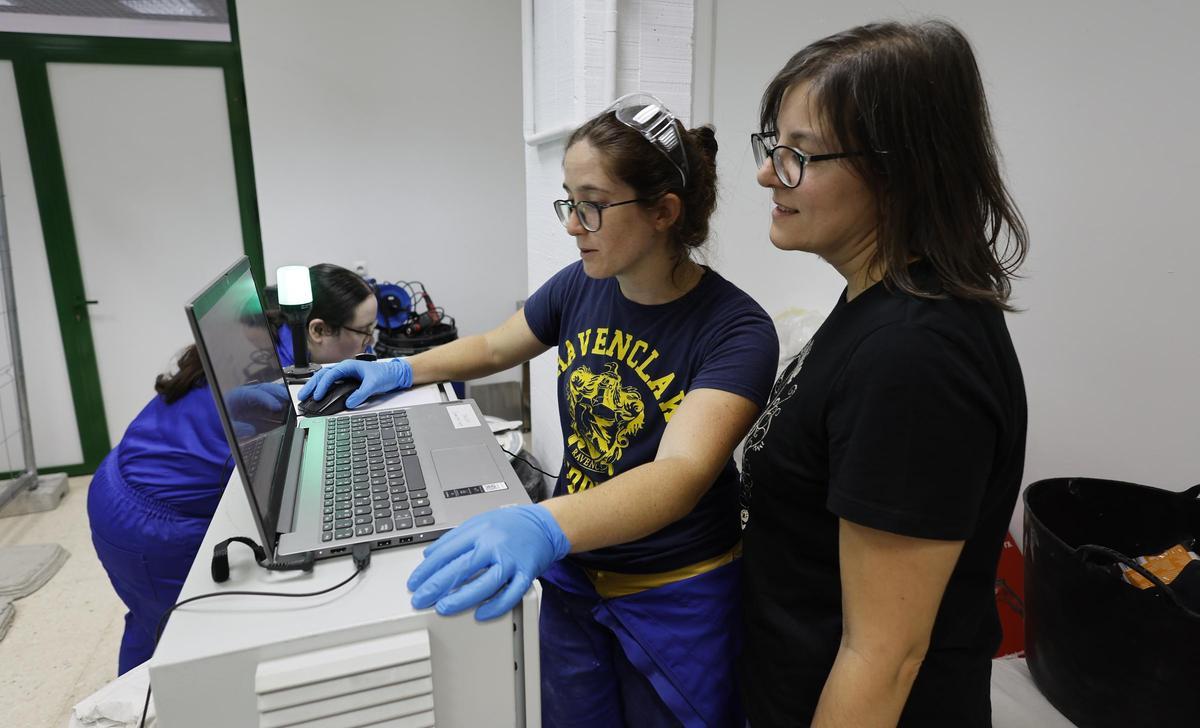
Carmen Mariño y Belén Díaz, en el punto de control de la impresora. / Ricardo Grobas
Durante los próximos meses, las expertas establecerán cuál es la mezcla óptima a partir de la evaluación de parámetros asociados a la cantidad o tipo de fibras de carbono utilizadas, la relación agua/cemento o la incorporación de aditivos, así como la velocidad de impresión, el diámetro de la boquilla o la presión empleada.
¿Y cómo se mide su eficiencia? Los investigadores tienen en su laboratorio pequeñas piezas de hormigón atravesadas por barras de acero que simulan las estructuras reales y que se conectan a una fuente de alimentación.
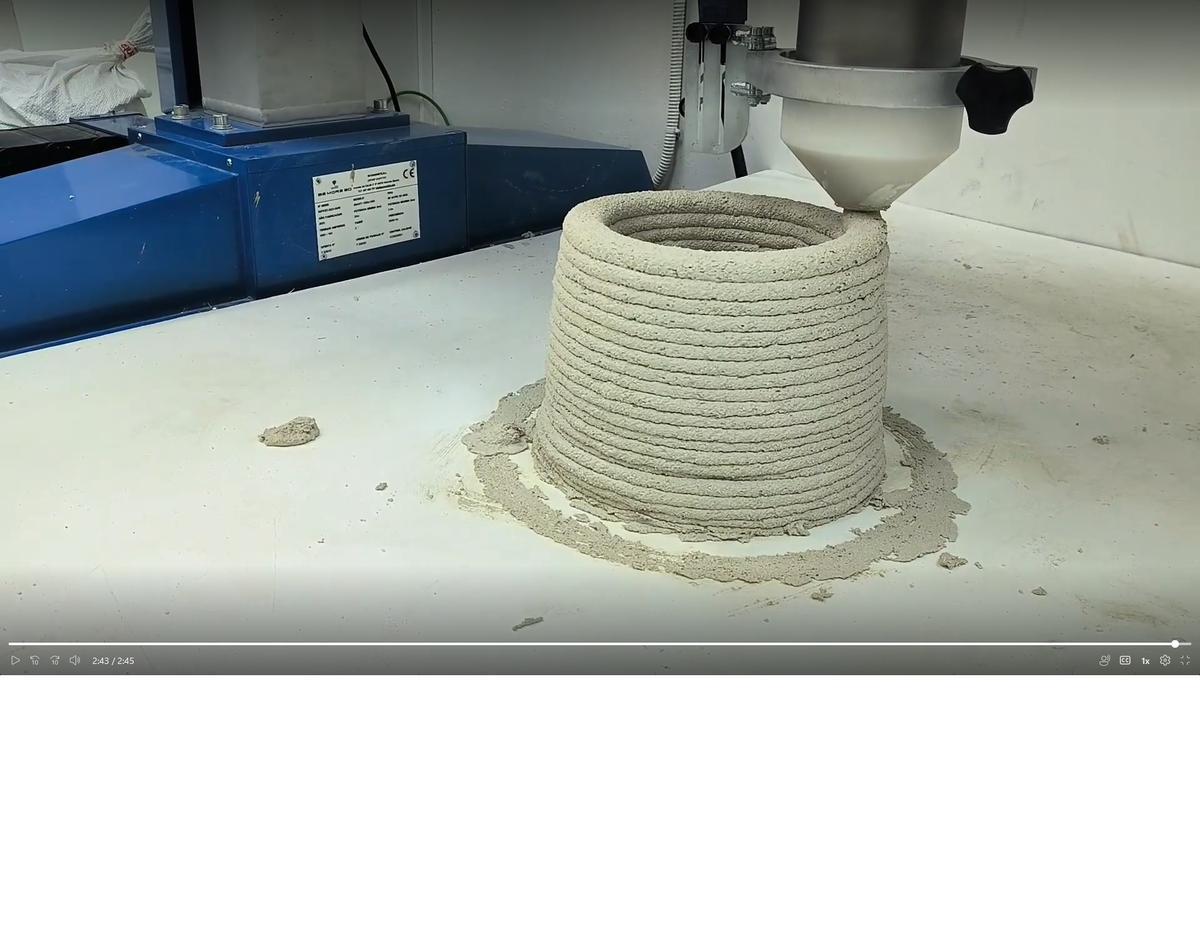
Fabricación de una pieza en el laboratorio de la UVigo. / Cedida
“Las técnicas de electroquímica nos permiten analizar qué ocurre en el interior de la estructura. Aplicamos corriente y, transcurrido un determinado periodo de tiempo, analizamos si la velocidad de corrosión sigue siendo igual, mayor o inferior. De esta forma, sabremos si las piezas 3D funcionan, si lo hacen mejor que las películas actuales y qué materiales son más efectivos”, explica Díaz sobre el desarrollo del estudio.
Convocatoria de investigaciones orientadas a la transición ecológica y digital
El proyecto fue seleccionado en la convocatoria de 2021 de investigaciones orientadas a la transición ecológica y digital. Y el objetivo final es alcanzar un protocolo de fabricación más efectivo y competitivo a nivel industrial frente a los actuales métodos convencionales de reparación basados en la preparación manual de electrodos de diversa naturaleza.
Las piezas 3D aumentarán la vida del hormigón, lo que tendrá su impacto en la producción de cemento y, por tanto, conllevarán una reducción de las emisiones de CO2 generadas por esta industria, que suponen el 8% de todas las que llegan a la atmósfera.
“Además de aportar conocimiento sobre nuevos materiales, nuestra intención es que el proyecto llegue a tener aplicación y esperamos que las empresas del sector o cualquier otro grupo de investigación muestre interés por los resultados”, expresa Belén Díaz.
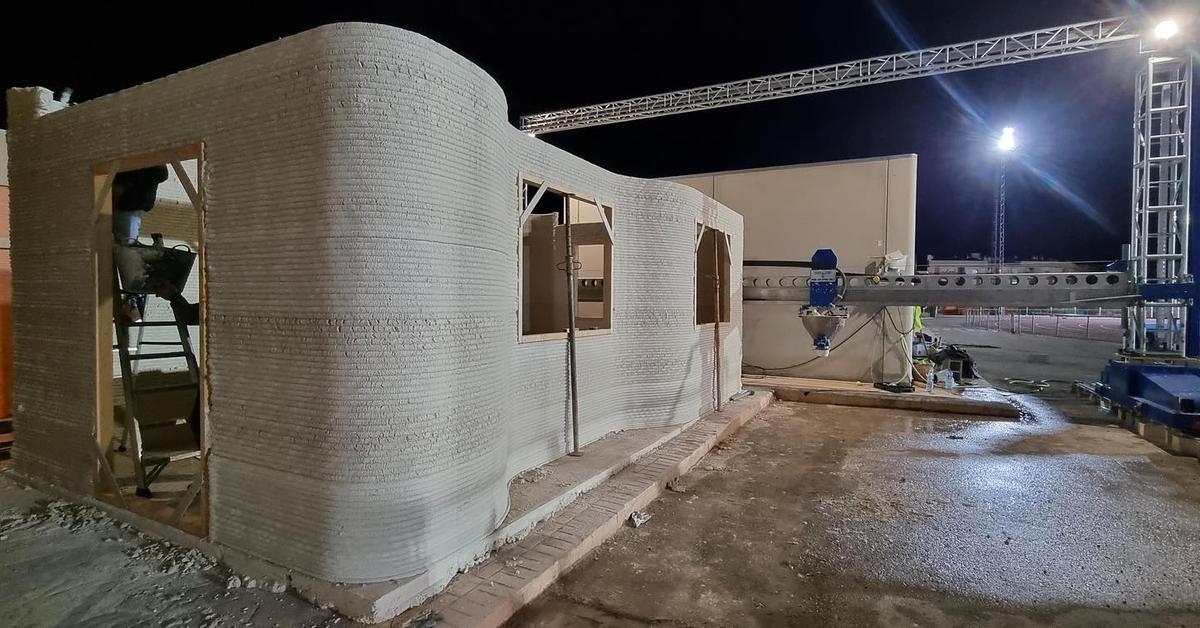
Una de los últimos proyectos de la empresa. / Be More 3D
La tecnología que fabricó la primera casa 3D de España
La empresa Be More 3D surge de la Politécnica de Valencia y está detrás de la primera casa impresa en hormigón 3D en España en 2018. El equipo funciona como una manga pastelera que va superponiendo capas que se funden en un muro o, en el caso de este proyecto, en piezas con distinta geometría. La máquina ha supuesto una inversión de 50.000 euros.
Suscríbete para seguir leyendo
- Los 'Mozos de Arousa' se despiden de 'Reacción en Cadena' con el tercer premio más alto de la historia de la televisión en el bolsillo
- Carlos Sobera, sorprendido tras conocer el trabajo de una soltera de 'First dates': "Espero no verte más
- Estos son los minutos que hay que caminar al día para conseguir adelgazar: muchos menos de los que te imaginas
- Este es el ganador del bote de 'Pasapalabra' que terminó en la cárcel de Teixeiro y perdió todo el dinero del premio
- Isabel Díaz Ayuso, de turismo por Galicia en plena polémica de los 'fodechinchos
- Bruno, de 'Los Mozos de Arousa', habla sobre su derrota en 'Reacción en Cadena': "Por fin cobraremos
- Así es la cena antiedad de la reina Letizia: adelgazante, nutritiva y muy fácil de preparar
- África y Alejandro, dos vidas segadas cuando empezaban a brillar